ご案内
●このサイトは、自由工房の2023年度までの活動を公開しています。
●2024年度からの活動は、*自由工房大学公式サイト*、*自由工房公式サイト*、でご確認できます。
トピック
2022年度 新メンバ募集!
プロジェクト紹介(PDF)と各競技説明
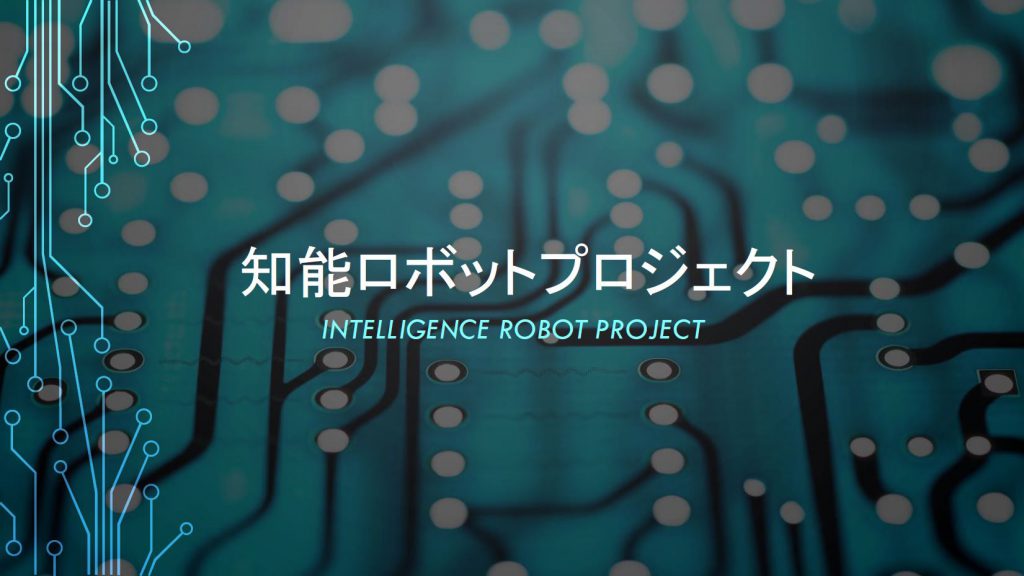
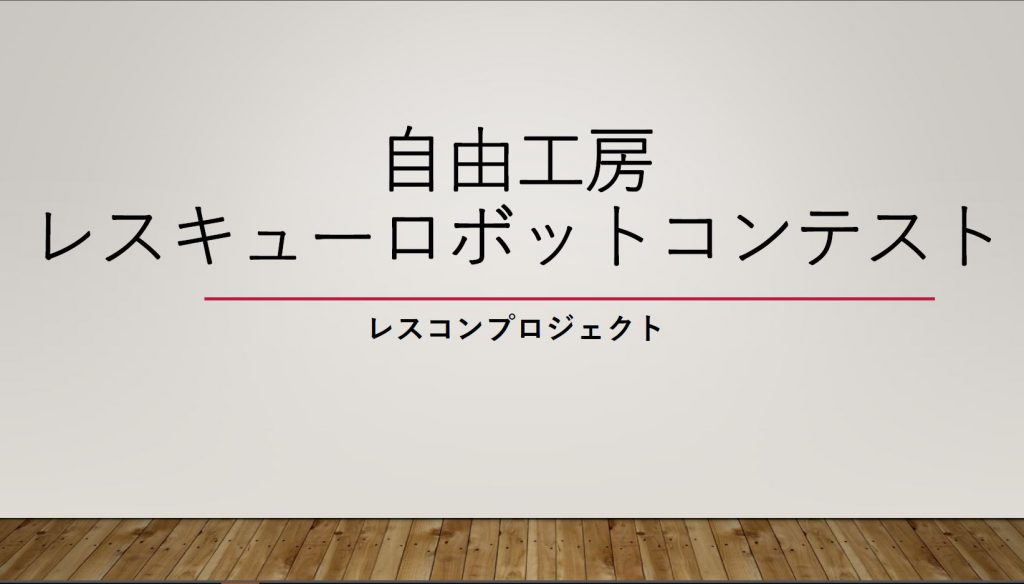

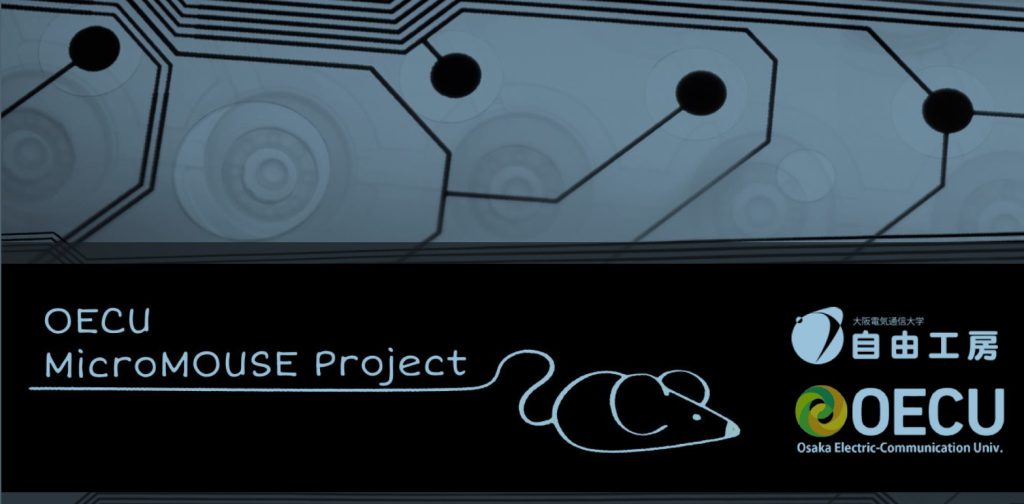
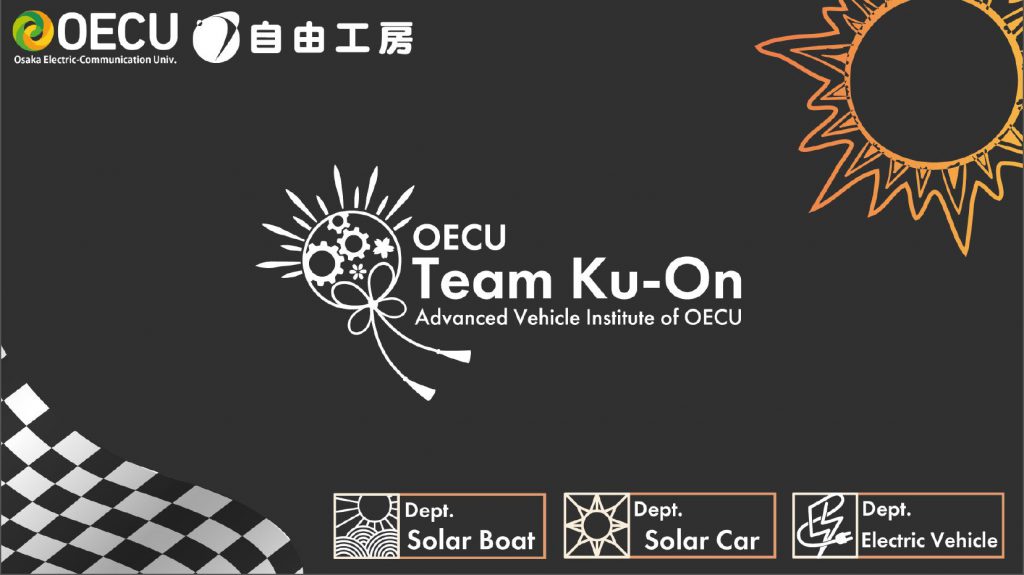
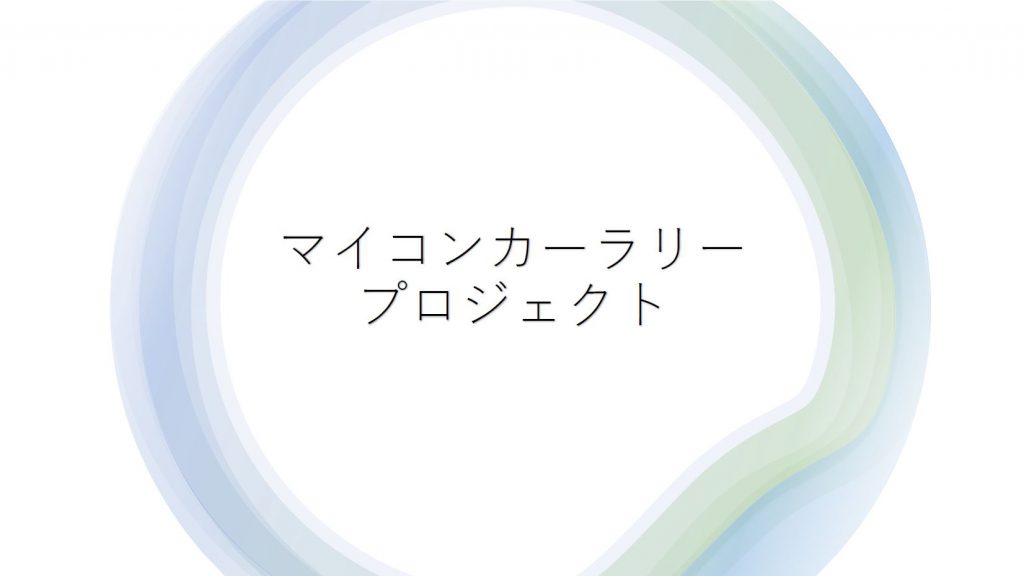
ヒト型ロボットプロジェクトは、四條畷キャンパス 2号館3階2-301号室 で活動しています。それ以外のプロジェクトは、寝屋川キャンパス Y号館502号室 です!
新規メンバー申込み・問合せ ( oecu.jp内だけで公開 中)
更新情報
2023.12.10:「第38回全日本学生マイクロマウス大会」レポート
2023.11.05:「ヒト型レスキューロボットコンテスト 2023」レポート
2023.11.04:「早稲田大学理工展ロボットフェスティバル」レポート
2023.10.29:「第32回(2023年)マイクロマウス九州地区大会」レポート
2023.10.28:「ロボファイト27 in ロボットストリート 2023」レポート
2023.09.24:「MISUMI presents 第42回ROBO-ONE」レポート
2023.09.03:「第36回マイクロマウス中部地区初級者大会」レポート
2023.08.12:「レスキューロボットコンテスト2023」レポート
2023.07.16:「2023年度マイクロマウス関西地区大会」レポート